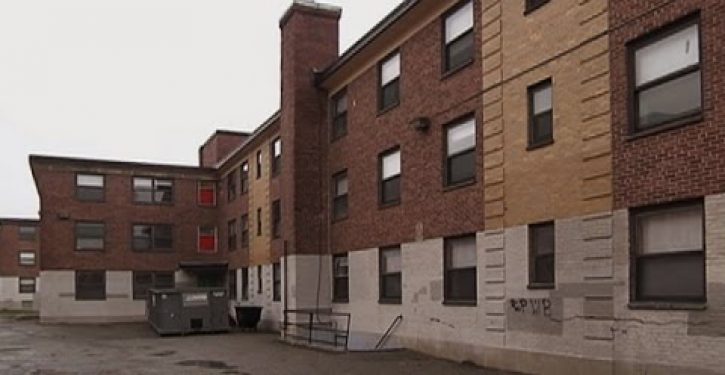
“A robotic truck equipped with a 105-ft (32-m) telescopic boom arm has just journeyed from Australia to Florida. Now the construction robot will get busy churning out up to 10 houses in a bid to become the employee of choice for building entire communities,” reports New Atlas:
The truck and its accompanying brick-laying arm is known as the Hadrian X and has been developed by robotics company FBR, which first announced its prototype in 2015. That machine could complete a full-sized house in two days. Last year, FBR (which used to stand for Fastbrick Robotics), showed off the new Hadrian X which, at top speed, could stack 500 USA-format masonry blocks per hour.
The robotic vehicle/construction arm gets to work after it is loaded by pallets containing the blocks. Each block is then sent down a chute on the arm, painted with a quick-dry construction adhesive that takes the place of mortar, and is placed by a variable gripper at the end of the arm. Thanks to its impressive length, the arm is able to build structures that are three stories tall. Plus, because it’s a robot, it never needs to sleep or take a break if the weather turns nasty, so it can chug along pretty much 24/7.
If the robot does well building 5-10 homes as part of a demonstration program, that will likely lead to the purchase of 300 of the robots from FBR, which will then be used to create entire robot-built housing developments.
Such robots could help fill the shortage of construction workers. As NAHB notes, “There’s a monthly shortage of nearly 400,000 construction workers, and builders will need to add 2.2 million new workers over the next three years to keep up with demand.”
It might also help cut costs. “The cost of building materials has surged 38% since the pandemic. Of particular concern, the price of distribution transformers is up 72%, and along with a severe shortage of transformers, this is delaying housing projects across the nation.”
Another way to cut costs would be to eliminate needless complex building code provisions. “Regulations account for nearly 25% of the cost of a single-family home and more than 40% of the cost of a typical apartment development.”
Housing is also expensive because of stagnant productivity in the construction sector. In most industries, productivity has risen enormously since 1947. But not in construction, where productivity has not increased at all over the last 75 years. As Market Watch noted in 2017,”While construction has appeared stuck in a time warp, other sectors have transformed themselves. Consider that in the United States between 1947 and 2010, agriculture achieved cumulative real growth in its productivity of 1,510% and manufacturing 760%…U.S. construction-sector productivity is lower today than it was in 1968.”
Why is productivity so low in construction? Partly because high-cost, low-productivity methods are promoted by federal housing regulations and subsidies. The Foundation for Research on Economic Opportunity (FREOPP) explains:
According to the U.S. Bureau of Labor Statistics, construction productivity in 2020 was 40% lower than in 1970, even though productivity in other sectors of the economy more than doubled during that time. While local regulatory policy is unquestionably a factor in this decline, FREOPP Visiting Fellow Jackson Mejia notes that restrictions on the methods of housing production also affect the supply of affordable housing. Prefabricated factory-built housing costs about one-third as much as traditional “stick-built housing,” but it constitutes just 10% of new single-family home construction today. In the 1970s, it was 60%. That dramatic decline is thanks to monopolistic government policies, from mortgage subsidies to federal safety standards, that irrationally favor stick-built methods over factory-built. To make more housing available to more Americans at lower prices, the federal government must get out of the way and allow housing construction to modernize the same way other sectors of the economy have.
Federal policies promote “‘stick-built housing,’ when buildings are constructed on-site by traditional construction methods. This method requires highly skilled, frequently unionized workers to produce homes on-site. Pre-fabricated factory-built housing, by contrast, costs about 1/3 as much per square foot”:
Research by economist Jim Schmitz at the Federal Reserve Bank of Minneapolis highlights that the prevalence of stick-built housing is a function of monopolistic behavior by construction companies and government policy, particularly the National Association of Home Builders (NAHB) and the Department of Housing and Urban Development (HUD). This happened in a couple of steps.
First, HUD developed Section 235 in 1968, a program that substantially subsidized mortgages on stick-built but not factory-built homes. Given the relative inefficiency of stick-built production, this program effectively subsidized a low-productivity technology at the cost of other, more efficient production methods.
Second, HUD and NAHB pushed the National Manufactured Housing Construction and Safety Standards Act of 1974 through Congress. The act effectively operates as a national zoning ordinance and restricts the production of factory-built homes substantially by requiring such homes to meet certain standards. At the time, factory-built housing competed with stick-built housing largely in low-density areas, many of which had no zoning laws to begin with. Before factory-built housing could make headway into urban areas, it was strangled in the crib.
Local building codes that vary from county to county and state to state make housing more expensive by preventing mass production of housing by factories. A factory can’t just come up with cheap, durable modular housing and then sell it everywhere. Imagine how much more expensive cars would be, if they had to be produced by hand in tiny factories located in each individual state or county, rather than (as is currently the case) being mass produced in large factories in a few states (in facilities that use robots and take advantage of economies of scale). The difference in requirements from place to place makes it hard for factories to produce housing that can be used in many places. That makes it hard to set up factories that produce large amounts of cheap, high-quality modular homes.
The net result is lower productivity in the construction industry.
Robots are improving productivity in other industries. Robots with artificial intelligence are spreading on Japanese farms. On some American farms, there are drones with artificial intelligence, and robots that use artificial intelligence to kill 100,000 weeds per hour. Scientists have developed tiny robots to repair damaged cells, and nanorobots to destroy cancerous tumors.